Large Diameter Floor Steel Silos for Powder Technology and Performance Overview
With the development of technology, the floor steel silos for powder show construction trend: bigger and bigger capacity of single silo; more and more complete function. As the capacity of steel silo increases gradually, the structure design, foundation form, environmental protection, natural factors (geology, hydrology, freezing temperature, etc.), unloading form, and energy consumption index, investment cost of single silo and other factors have to be considered by the construction party.
Floor steel silos have been widely used in the field of storage, transportation and transfer of materials because of their larger capacity, higher land utilization, higher automation, shorter construction period and lower investment per silo.
After continuous development, FLYER has completely solved a series of technical problems about the material accumulation in the edge room inside silos, the lower unloading rate, bad homogenization effects and hard maintenance and replacement of the inner equipments of large diameter of silos. Through the applied experiences of a number of large enterprise groups, our products are effectively confirmed and recognized by the users at home and abroad. The practices prove that the unloading rate has reached more than 95% according to all the data of the different diameters and different numbers of unloading holes of silos. In the meanwhile, as the silos are in the storing state, the users still can be convenient for the maintenance of gasification equipment.
Objectively speaking, the steel silos manufactured by FLYER Company have fully features of large capacity, investment saving, faster construction speed, higher unloading rate, good homogenization performance, lower energy consumption, safer and more reliable operation performance, automatic control, longer service life and so on.
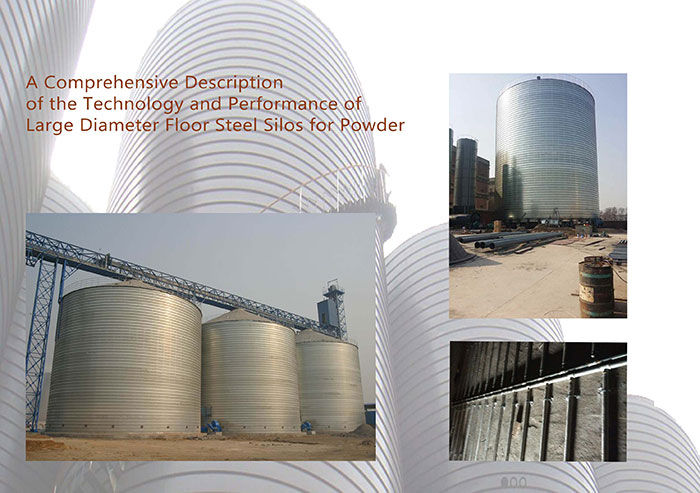
14 features of Flyer steel silo tell you how to distinguish the better silo
1. Perseverance boost pressure technology: adopting the principle of the perseverance boost pressure to design the ring foundation of the silos can adapt the construction in different geological conditions.
2. Shape and size of the silo structure: the large steel silos belong to a large thin-wall vessel with the about 1:1 ratio of height to diameter. Their silo bodies are cylindrical with hemispherical roofs. Their unique architectural structures can make reasonable construction structure of the roof dome have a reliable bearing capacity.
3. Loading method: according to the requirements of the users, we can adopt the conveying method of the pneumatic transmission by the pipes or mechanical transmission to load the silos using the central loading method on the roof.
4. Unloading principle and description: the size of the unloading pipe is decided by that of the diameter of the silo body. When the material is filled with the steel silo, we can open any valve we need to make the material move smoothly under dual functions of pneumatic force and gravity.
5. The material pressure shall be evenly distributed in the base plate of the silo. The pressure will be transferred to the ground through the silo floor, realizing the pre pressure bearing. This should meet bearing capacities of different foundations. The floor shall be filled with light pressure resistant materials. The fluidization device shall be arranged on the fillings. Every set of device is an independent unit, which can timely realize necessary replacement of the external devices in the state of material storage. When unloading and conveying of the material, the Roots blower or air compressor machine can keep sure of air supply. After the fluidizing device has been inflated, the material will flow smoothly and be unloaded to the pipe in the conveying device. The pneumatic conveying of materials can achieve the dense or dilute unloading of the material. The users can adjust the dividing wheel of the variable frequency speed governor to control the material transportation. The whole system can be operated by local automatic control and centralized control. This technology uses double combination technology of gravity and pneumatic unloading & conveying in non-inflatable state. The gravity unloading and conveying can greatly reduce energy consumption. As unloading and conveying, air sources should each be equipped with a low pressure Roots blower without any operation of the equipment in the silo, which can reduce maintenance cost.
6. The stable operation is easy to realize automatic control. The uniform and stable unloading process will not appear the various dangerous phenomena to ensure the use safety of silos. This is easy to realize automatic control for the sequences. Automatic control cabinet can help to achieve local, manual, automatic and computer control.
7. Because the silos use the designs of the fluidization unloading, homogenization, the integration of unloading & conveying, air consumption is small.
8. The storage effect of the material: the material is basically stored in the air isolation state. The sealing performance of large steel silo is close to vacuum. The storage effect of the material is better than other structural storehouse, for example brick, stone, concrete, etc.
9. Environmental standards: the silo roof is designed of bearing dome. On each roof there provides with a pulse dust collector that can collect main dust in the material unloading process.
10. Layout: according to the site conditions, the silos can be flexible designed in the layout. The direction of unloading pipe can be determined according to the site. Because of the use of pneumatic unloading, the position of the hoister can be free to choose.
11. Short construction period: the construction period is short. The construction of the group silos can arrange cross construction so as to shorten the construction period.
12. Long service life: a unique combination can improve the safety of the silo body. The frame structure is similar to the structural building, so the silo has stronger earthquake resistance, deformation resistance and bearing capacity of the body.
13. Low maintenance cost: there is no corresponding operating components of gasification, unloading, conveying equipments inside the silo, which basically belongs to free maintenance.
14. Easy to safety maintenance: do not need to have the clearance. The users can facilitate the fluidization rods to do the maintenance.
FLYER Company has rich experience in construction of modern large spiral steel silo for powder. If you have any problems or requirements, please contact with us freely. We will provide you with relevant specified information. Expect to set up sincerely friendship with you!