How to Prevent Hardening of Fly Ash in the Steel Silo?
The modern large steel silo has been pretty optimized in design, which is divided into several positions in the unloading area. Each position stands for one unloading point with 1m2 outlet area, whose slope angle is not less than 17°, or even reaches 50° in some special positions. On the slopes the fluidized bars are installed; On the silo wall annular fluidized bars are installed. And generally there are more fluidized bars to be set on the slope of the silo wall to outlet. These make the whole silo no dead space so that the emptying rate of the silo can reach more than 95%. Moreover, new pneumatic unloading system is adopted popularly now. In the design a 10-50 thousand ton of the silo will have one unloading hole, more than 50 thousand ton of the silo will have four unloading holes. Adopting frequency conversion technology, most unloading capacity can reach about 500T/H.
Even so, it is difficult to avoid 100% hardening problem. The reason of hardening of fly ash silo may be caused by several reasons: first, the leakiness of the silo. The fly ash absorbs water in the air from the places that the ash silo is not tight for a long time; second, the design defects of fly ash silo. At the inlet of fly ash silo, diversion device should be designed to avoid one position loading. Due to heavy weight and inertia, the lower part of the fly ash is often compressed into the blocks; third, fly ash silo is manufactured by low quality of steel quality, especially its thickness is so thin that fly ash in the silo is easy to absorb moisture in the air.
If you are trouble in the above problem, how do you deal with it?
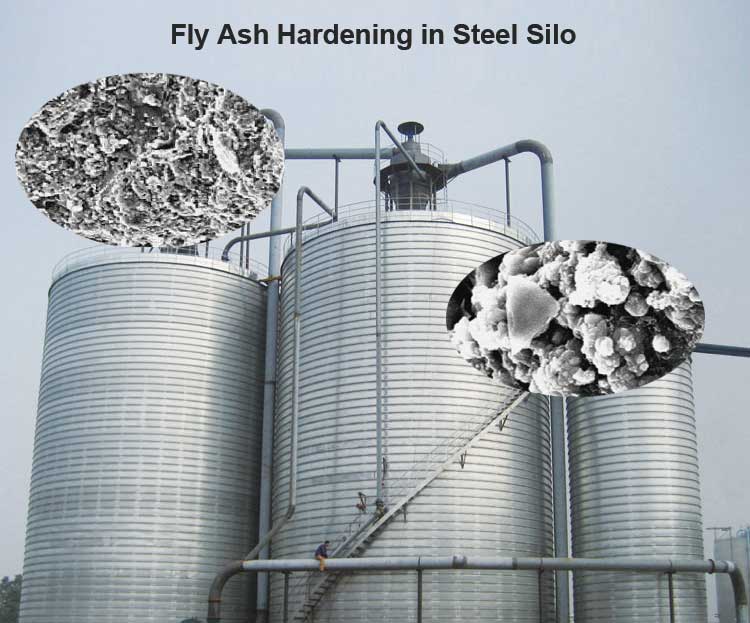
Precautions of Fly Ash Steel Silo
First, in the long-term storage process of fly ash, it is not content with too much water before storage. And the bottom of the silo must be implemented waterproof processing. The ash in storage for a long time should do regularly homogenization, which is generally appropriate 2 to 3 times a week so that it can achieve good effect.
The ash in the silo is the best to be installed with the fluidized bars that are more effect in the bottom than the inflatable box. The homogenization effect rate of the fluidized bars can reach above 95%.
According to our inspection experience of the steel silo on site, the main reason is that gasification homogenizing device of the bottom plate of the silo may cause unsmooth unloading, leading to seriously affect the normal production needs. In view of the above situation, combined with our many years of construction technology and experience for similar engineering silo, we shall formulate the following construction plans.
Technical Measures of Fly Ash Steel Silo
Due to the long time of silo storage in operation, the silo forms the blocks that results in the blockage at the bottom of the silo.
First, construction workers enter the silo from the roof to check the situations of the resting ash and its hardening degree. The first step is to use the air gun in the silo bottom to fill air and get the ash to be self loading by gravity. If gravity cannot have good effect, the workers start to enter from the side gate of the steel silo. The construction workers first install chute device at the side gate. The resting ash will be smoothly unloaded from the silo to the tank vehicle. If a block of accumulated material is unloaded out from the silo, it should be transported to be elsewhere as the pre-arrangement in order to prevent the impact of normal construction. If the outlet cannot works normally, we need to do a temporary unloading chute for cleaning ash. When the vacuum cone inside the silo is exposed, and we should stop unloading and then open a 400mm×500mm of hole to help construction workers to enter and clear the unloading outlet at the bottom.
Before the construction, construction workers must take safety protection measures and make fully protection preparation well. The construction workers generally choose the Φ18 palm rope or nylon rope as the safety rope. One end of the safety rope is fixed on the silo roof. The other end is tied on the workers at the waist. In order to construction safety, the workers should learn to guard themselves, who also usually tie another Φ18 palm rope or nylon rope with 10m in length at their waists to ensure the safety in the construction process. Entering the silo, the workers firstly do their own safety work that is to fix the other end of the safety rope on the waists and make safer. And then they will check the distribution of the fly ash. The workers outside the silo will deliver necessary construction tools through the Φ12 palm rope to the bottom. After getting the tools, the inside workers begin to work as the cleaning sequence of high to low. When the cleaning work is close to silo bottom gate, the workers can enter it from the small silo door at the bottom. The inside workers get touch with the outside workers through interphones as the communication tools.
Safety Measures of Fly Ash Steel Silo
- Due to the suspension working, we always stick to the principal of safety first and prevention first. All the workers shall be in strict accordance with the overhead working procedures.
- The safety supervision departments shall have on-site safety training.
- The overall safety supervisor shall be responsible for the construction safety of the sky and ground with a security officer. All construction units must obey the safety supervision department that has the right to carry out the corresponding punishments.
- Before the daily work, the supervisor shall keep a technical train record of the safety operation to workers.
- All the construction machinery, the ropes and tools must pass the inspection before the workers’ entering into the silo.