How to Prevent Dust Explosion in Steel Grain Bin
The dust explosion in the steel grain bin has always been a problem of safe operation in grain processing enterprises and bulk grain handling systems. It will not only bring environmental pollution but also cause serious casualties and economic losses. Therefore, it is necessary for us to find out why it happens and take effective prevention and control measures.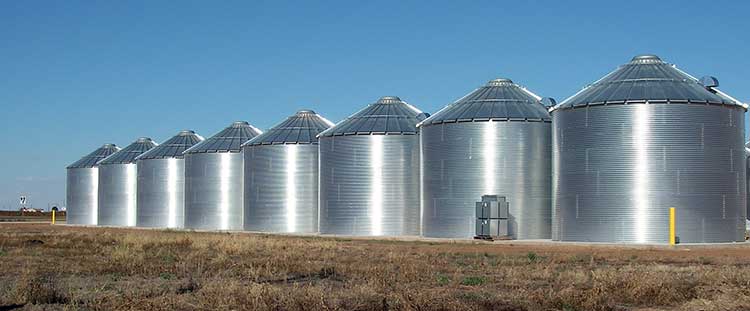
Hazards of Grain Dust Explosion
In the process of grain cleaning and transporting in a steel grain bin, a large amount of dry dust (moisture in the range of 11% ~ 15%) is generated. When the dust is fully mixed with air, it will be in a state of floating and aerosol. Although it is difficult to suspend in the air for a long time, many parts of the grain silo will always maintain a high dust concentration during the working process. Besides, the dust accumulated in some places of the equipment and steel silo, once affected by an external force, will re-enter a suspension state so that the risk of explosion always exists.Once the dust air mixture we mentioned above is ignited in a closed steel silo, the air pressure in the silo will increase sharply, and the propagation speed of the combustion wave is accelerated, which will be more than 300m / s, even up to 1000m / s. These velocities can form powerful shock waves, causing great damage to the surrounding objects, at the same time, spreading to other parts along the ventilation pipe or conveying equipment, forming a series of explosions. As to the harm degree of dust explosion, we can draw a conclusion by comparing the combustion heat of grain dust and solid explosives:
Data | Solid Explosives | Ignitable Dust | |||
TNT | Nitroglycerin | Corn Dust | Wheat Dust | Soybean Dust | |
Combustion Heat (Kcal·kg ) | 1210 | 1510 | 3200 | 1650 | 1830 |
Maximum Explosion Pressure (Mpa) | 0.75 | 0.81 | 0.82 | 0.78 | 0.82 |
Causes of Dust Explosion in Steel Grain Bin
There are many causes for dust explosion in steel grain bins, which can be mainly divided into management factors, process design factors, and dust physicochemical property factors.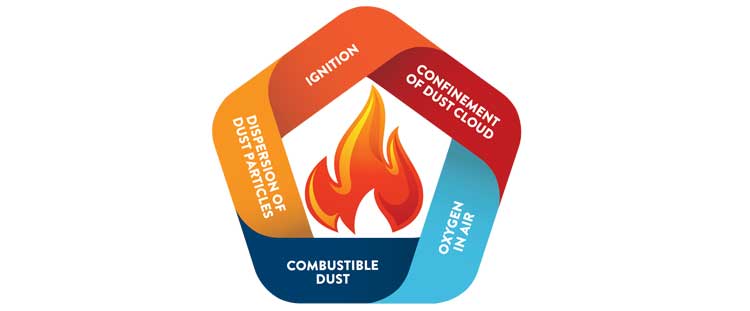
Management Factors
- Managers and operators lack basic knowledge of fire and explosion protection and do not pay enough attention to it.
- Open fires occur in steel silo operation areas, such as smoking in the workplace, throwing cigarette butts, etc.
- Improper operations during equipment maintenance and replacement. Operators are failure to take necessary safety precautions.
- The dust accumulation inside and outside the equipment is serious.
- There is no explosion vent designed and no enough firefighting access.
- Excessive content of dust, stone, and metal impurities in grain.
- The dust removal process is not reasonable so that the dust concentration in equipment and pipelines is high.
- Improper selection of equipment, or with no reasonable fire and explosion protection measures
- Generally, dust particles with size less than 10 μ m are easy to form aerosols with the air and float in the air for a long time. In grain silo, the grain dust smaller than 10 μ m accounts for 20%, which causes a high dust concentration inner the silo.
- The air flow and equipment vibration will make the dust settled on the equipment and building structure rise again, thus increasing the possibility of explosion.
- The organic content of grain dust is more than 40%. When it meets an open fire, it will burn. Therefore, in a closed steel grain bin, as long as the dust concentration reaches 40g / m3, there could be an explosion.
Precautions for Grain Dust Explosion
Scientific Management- Train operators to master the basic knowledge of dust and explosion protection.
- Operators should check the running of silo equipment frequently and take necessary measures immediately if any abnormalities are found.
- Prohibit all open fire into the silo operation area.
- Keep the equipment surface and ground clean.
- Be sure to have firefighting equipment in the silo area.
- The process design should be simple, efficient, and flexible. Then the times of friction and impact will be reduced and the dust generated will be less.
- Install a magnetic separation device in front of the primary cleaning equipment, bucket elevator, scraper conveyor, electronic scale, and other equipment to remove metal impurities in grain, so as to avoid sparks caused by the collision between metal impurities and some parts of conveying equipment during grain transportation.
- The linear speed of the bucket elevator and scraper conveyor should not be too high. Otherwise, the bearing temperature will rise, once the ignition point of dust is reached, an explosion may occur.
- Install a temperature sensor at the bearing of high-speed running equipment to monitor the temperature in time.
- The filter bag on dust collector and the belt on bucket elevator should have good conductivity to prevent electrostatic accumulation.
- Reasonably design the dust removal air net and ventilation system to reduce dust concentration in grain silos.
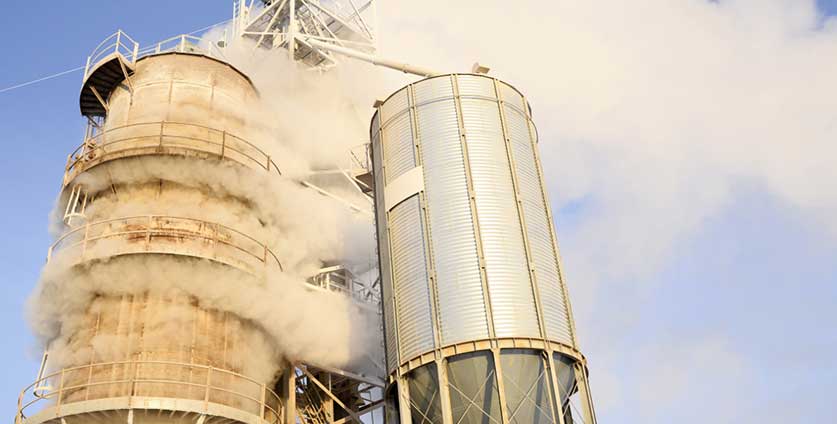
Explosion relief mainly refers to setting explosion vents on silo explosive equipment or pipeline. When a dust explosion occurs, the pressure can be released by breaking through the vent, thus reducing the damage degree of the explosion.
Get In Touch With