How to Choose Steel Silo’s Auxiliary Equipment
Importance of Choosing Proper Auxiliary Equipment for Steel Silos
The selection of auxiliary equipment is crucial part of the whole steel silo project. For example, both buried scraper conveyor and belt conveyor could be applied for horizontal conveyor. But which one is better? The final choice should be based on the careful analysis and comparison of the advantages and disadvantages between the two types of conveyor. The advantages of buried scraper conveyor are multiple-spot discharge, good sealing performance, but belt conveyor can not achieve. So it is more suitable to choose the buried scraper conveyor on the top of the steel silo. However, the belt conveyor keeps the advantages of reducing the crush of the material, long-distance transmission and low power cost. So for the industry which demands high on material crushing, such, like wet grinding starch industry, belt conveyor is more suitable than scraper one. What’s more, in the design of many large port steel silo projects now, long-distance inclined belt conveyor is more frequently applied than bucket hoist conveyor for its better reducing the crush of materials. In this way, the quality of material could be highly guaranteed, although the investment may be increased a little.
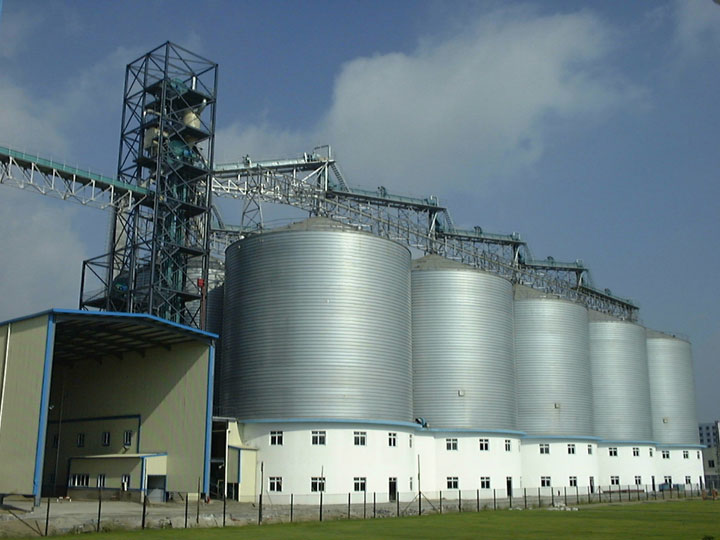
That is why to say the selection of the steel silo is very important in the process design. Inappropriate equipment can not meet the requirements in design process. What’s worse, it may cause irretrievable losses.
Some Suggested Methods on Selecting Auxiliary Equipment for Steel Silo
- First, the production of selected equipment should match with its function. Selection for equipment’s delivery value depends on the capacity of the steel silo and its quantity to import and export grain. The capacity of grain export should match the main workshop. Equipment with too large capacity is a waste of equipment investment with high operating costs. On the contrary, equipment with too small capacity will cause a retention phenomenon. Take the grain steel silo project on port bulk as an example, general type of seagoing vessel is between 5000tons to 6000tons. The output capacity are usually designed by 1000t/h to meet the ability of ship loading and unloading. Otherwise it will cause stranded phenomenon. In the grain and oil processing factory, the capacity of equipment depends on the ability of the car unloading. Generally, the efficiency of unloading sacked grain is low with a small output, when the efficiency of unloading loose-packed grain is high with a large output.
- Second, the sufficient space for maintaining on steel silo equipment should be considered previously: maintenance space of steel silo equipment is an important factor in the process design. Because the steel silo equipment needs the normal care and maintenance, so it requires adequate space for the operators to carry out maintenance work like replacement of bearings and cleaning sieve tube, maintenance of the TV reduction gears, etc.
- Third, the location of the electric control room should be selected carefully: it is better to set the electric control room up in a separate room, such as in a tower or under the steel silo, where is closed and dustless. Otherwise, the service life of the electrical parts would be affected by dust, and even serious safety accident may be caused.
As suggested above, you should make comprehensive consideration on selecting auxiliary equipment. Choose the most suitable one for your steel silo and give it a longer service life.