The Protective Measures of Atmospheric Corrosion of Steel Silo
As we know, steel silo is made of steel plate and section steel by welding, riveting or mechanical rolling methods for the connection. That is, raw materials of steel silo are ordinary steel products.
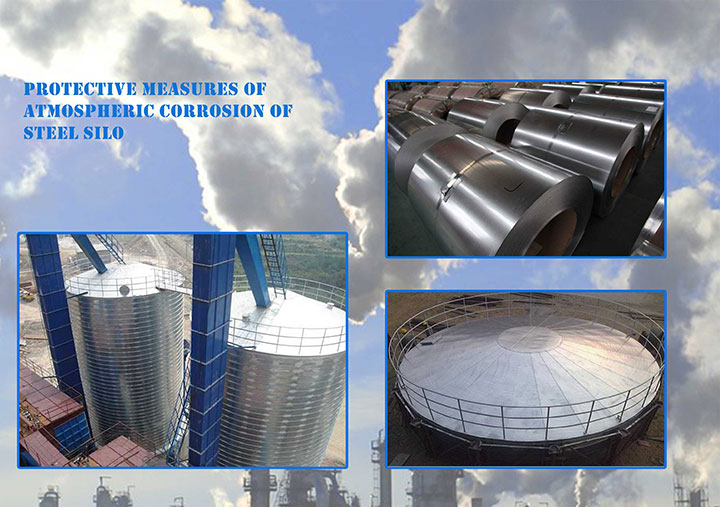
The atmospheric corrosion is the earliest corrosion type recognized by human. This is because the most of the metals and their products are mostly stored and used in atmospheric environment, for example, steel silo, steel bridge, railway, machinery, vehicles, electrical products, weapons, equipments, etc. Compared to other types of environmental corrosion, the atmospheric corrosion is one kind of more widespread phenomena. Wherever it is indoors or outdoors, the metal will be impacted by the atmospheric corrosion. According to relevant statistics of atmospheric corrosion, the loss of metal accounted for more than half of the total amount of corrosion. Flyer Company hereby puts forward some corresponding protective measures on atmospheric corrosion of steel silo. We hope that they can help every client.
Select the materials rationally according to local atmospheric conditions
1. The overall design on basis of local atmospheric conditions
When we make the overall design of the structure and strength of new steel silo, we must take the corrosion resistance measures according to local atmospheric environment and expected service life of steel silo. This Includes reasonable selection of raw materials, anti-corrosion design of water diversion groove of silo cover to avoid water accumulation. The surfaces protection and local reinforcement of the fastening bolts, nuts, clamping plates and rainwater gutter on the cover should be carried out according to the specifications, construction standards and anti-corrosion design service life. These maintenance designs should be included in the overall design of new steel silo.
2. Reasonable selection of raw materials
In order to prolong the service life of steel silo, we shall adopt appropriate galvanized sheets with certain zinc coating thickness as basic structure material. In order to obtain the galvanized zinc coating with a certain thickness, the sand blasting is more suitable than surface pickling before the use.
The correct construction of local reinforcement protection
1. Correct construction
In the construction processes of prefabrication, transportation, loading and unloading and on-site installation, it is necessary for us to avoid mechanical surface damage such as scratching and biting on galvanized steel plates, especially to avoid a large area of exposed steel damage.
2. Local reinforcement protection
Some parts in the overall structure may be lack of certain protection, such as weld areas and bolts & nuts. The latter usually cannot reach enough thickness of galvanized layer due to the limits of their assembly sizes. The weak parts still include the biting area of the galvanized plates and the channel steel in the wet state supporting the stiffeners of the cover on the silo roof. The painting materials, such as zinc (or aluminum) for thermal spraying, zinc-rich paint or neoprene paint, they are subject to be done regular maintenance to ensure the overall long life.
In summary, in order to make steel silo especially in corrosive atmospheric environment strong enough to obtain a long service life and low maintenance cost as much as possible, the corrosion protection measures are the key factor. We should make perfect overall design and comprehensive consideration, and then take a series of technical measures in the key links of material selection and construction process. As long as we make sufficient preparation and strict implement, the performance and the service life of steel silo has be fully quality assured.
Quality problems we should avoid
1. Choose wrong maintenance plans
After the half-year use, the steel silo shall be inspected whether there are widespread exposed steel spots on galvanized steel roof arising from the corrosion or not. If yes, we can make the surface pretreatment of rusted phosphatization. Specifically, the maintenance plan is that painting iron red epoxy primer two times and then painting acrylic modified alkyd resin paint as the finish two times. There are the following problems in this plan: first, no successful precedents; second, according to the international standards, steel surface must thoroughly remove residual paint by sand blasting / epiphyte. When it reaches Sa2.5 level, we can paint again. Taking the rusted phosphatization method instead of sandblasting surface pretreatment is not a good pretreatment method because we cannot guarantee good adhesion between the metal substrate and coating layers.
2. Bad construction technology
If the construction period of surface painting is in winter, the weather like rain, snow, ice and frost is frequent. Between the procedures, only using a rag cloth to clean cannot guarantee thorough dryness between two coating surfaces. Therefore, the environmental condition under the paint film will help form the corrosion with the rapid development.
3. Lack of quality supervision and control
It is understood that for the maintenance of the cover of the silo roof, if the implements do not confirm to national and international standard of surface pretreatment and any quality supervision and quality inspection after the construction is lacked, this will bring about a series of serious problems. The abundant practical experience has been shown that without QC/QA coating, we cannot not only expect it to provide adequate protection to the steel silo, but also cause more serious damages.
Nowadays due to environment pollutions, the composition of the atmosphere with a lot of toxins, the corrosion for the buildings is more serious, especially the gas sometimes contains strong acid and alkali which can directly make the building fully damaged. Under the combined actions of these above factors, the early corrosion and damage of the steel silo will inevitably lead to certain economic losses and adverse social impacts.
Steel silo is a kind of very good building for storing materials. It needs relatively high atmospheric environment requirements, so the corrosion protection of steel silo is the most important task for us.
FLYER Company has rich experience in construction of modern large spiral steel silo. We can effectively solve complex corrosion resistance problems you met. If you have any problems or requirements, please contact with us freely. We will provide you with relevant specified information. Expect to set up sincerely friendship with you!